This year’s International Freezer Challenge brought together a record number of laboratories from around the world, amplifying the collective impact of sustainable cold storage practices.
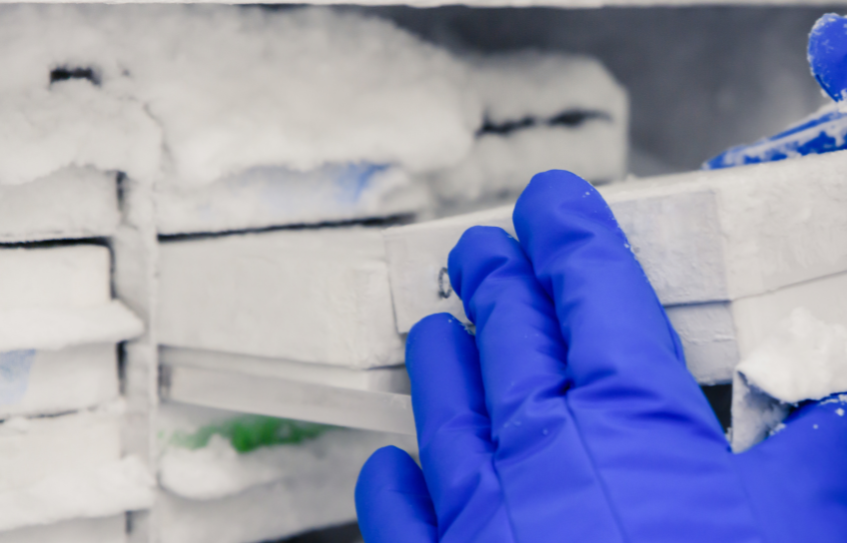
Greenwashing isn’t just bad for the planet; it has become a major financial and reputational threat. In today’s climate-conscious economy, companies are facing increasing, and often warranted, scrutiny from regulators, consumers, and investors.
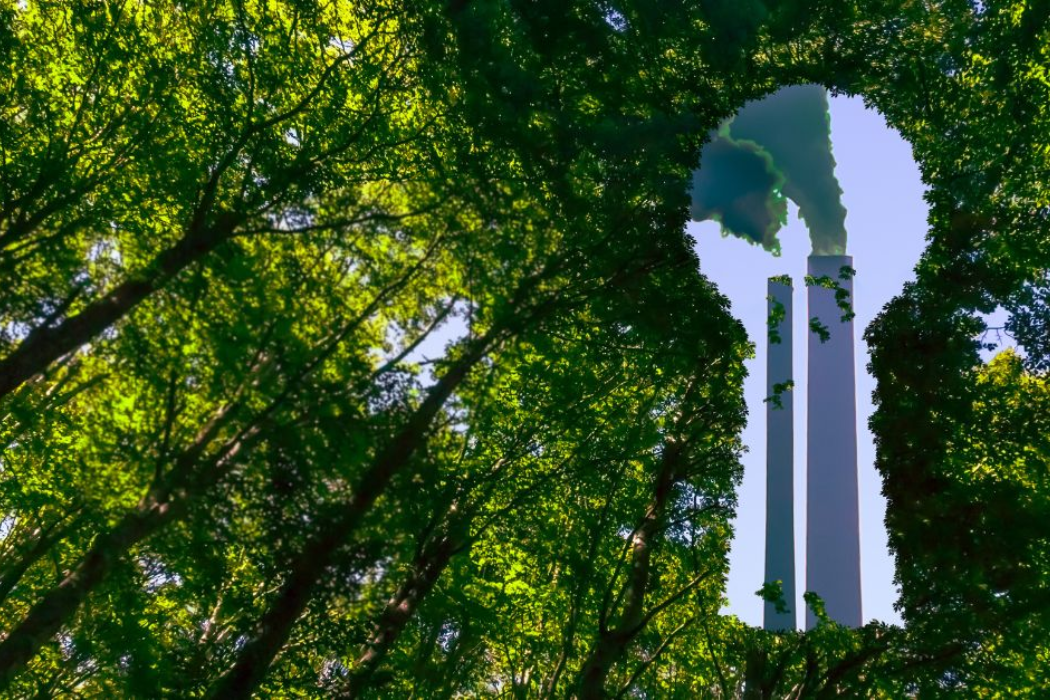
My Green Lab is proud to announce that our Converge Supplier Initiative has been endorsed by the Pharmaceutical Supply Chain Initiative (PSCI).
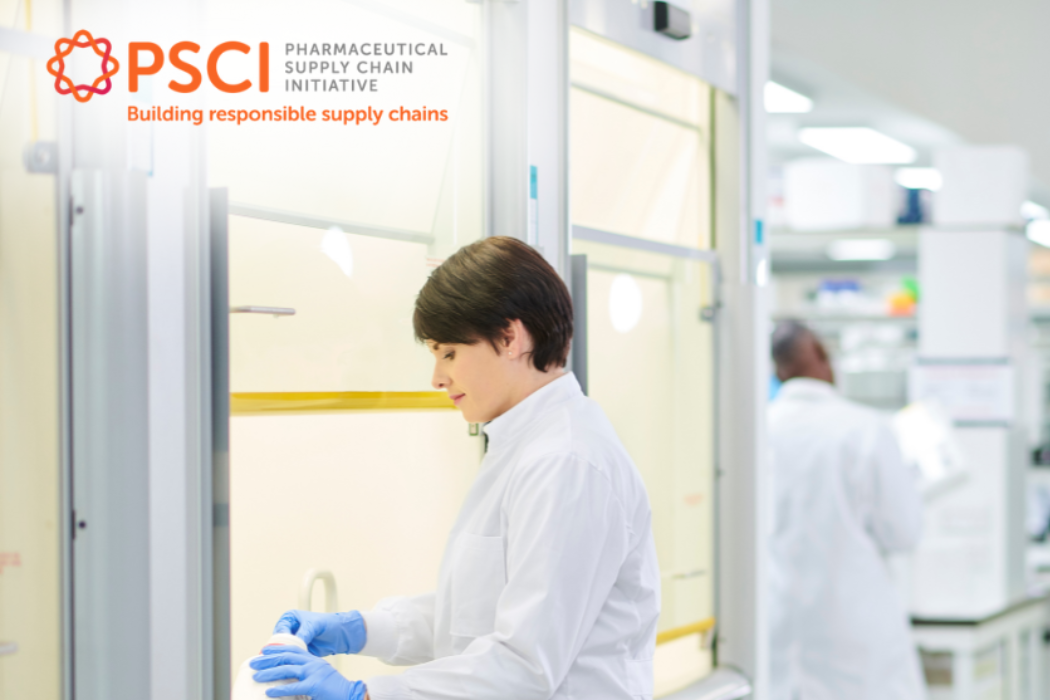
Whether you're just starting your sustainability journey or looking to deepen your lab’s commitment to sustainability, here are 8 impactful actions you can take today to improve energy efficiency in the lab.
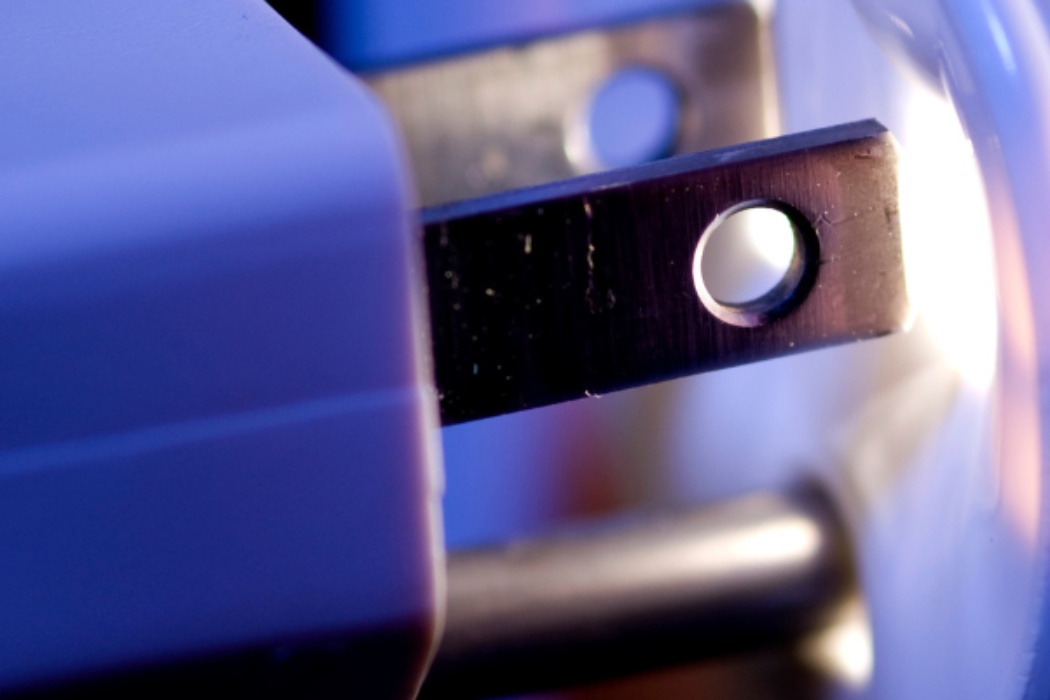
We are thrilled to announce the launch of the ACT Ecolabel 2.0 program, an enhanced version of the only third-party verified ecolabel for laboratory products!
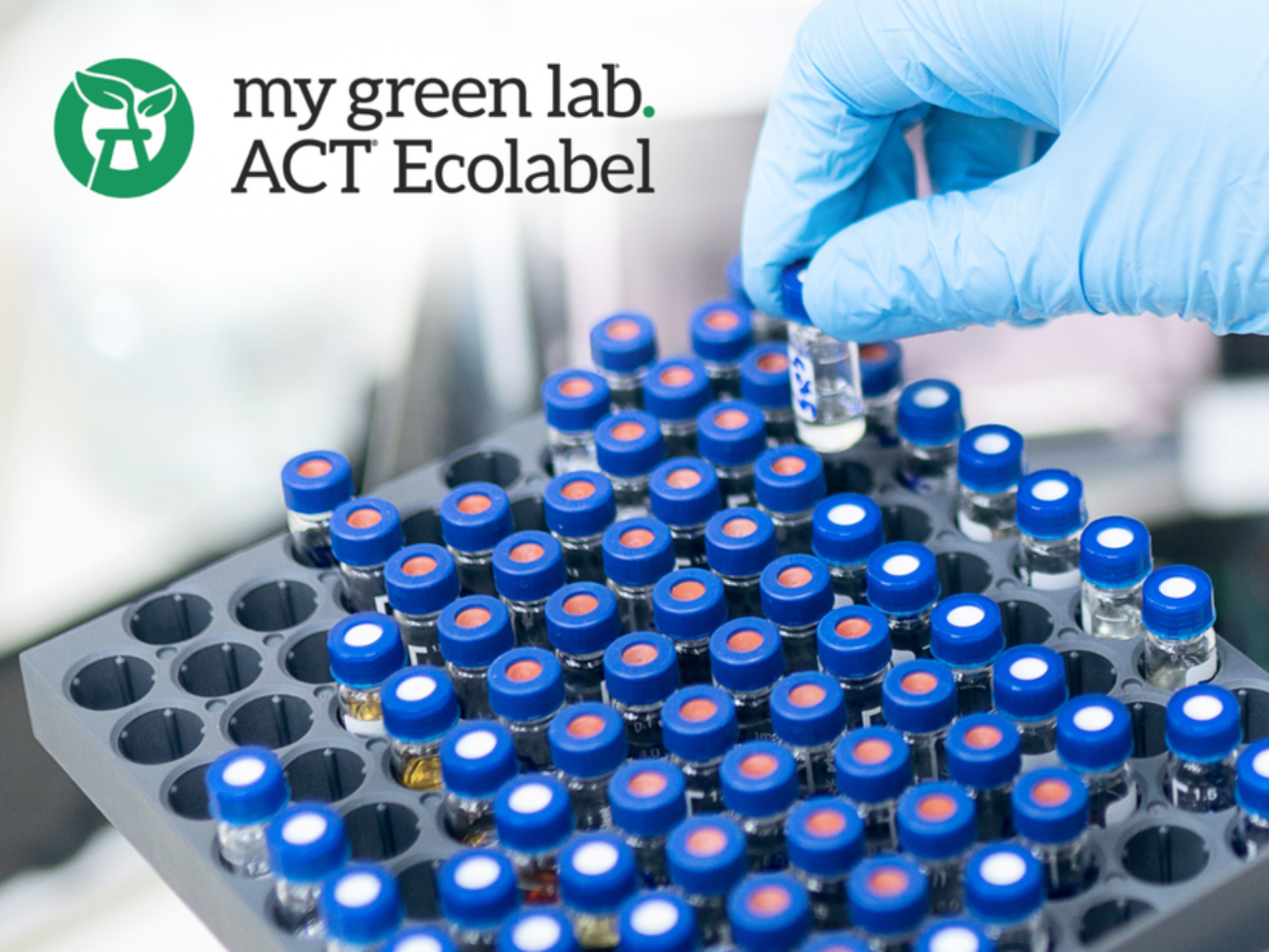
Amid the many environmental challenges we face, there are also incredible stories of innovation, resilience, and meaningful change happening all around the world.
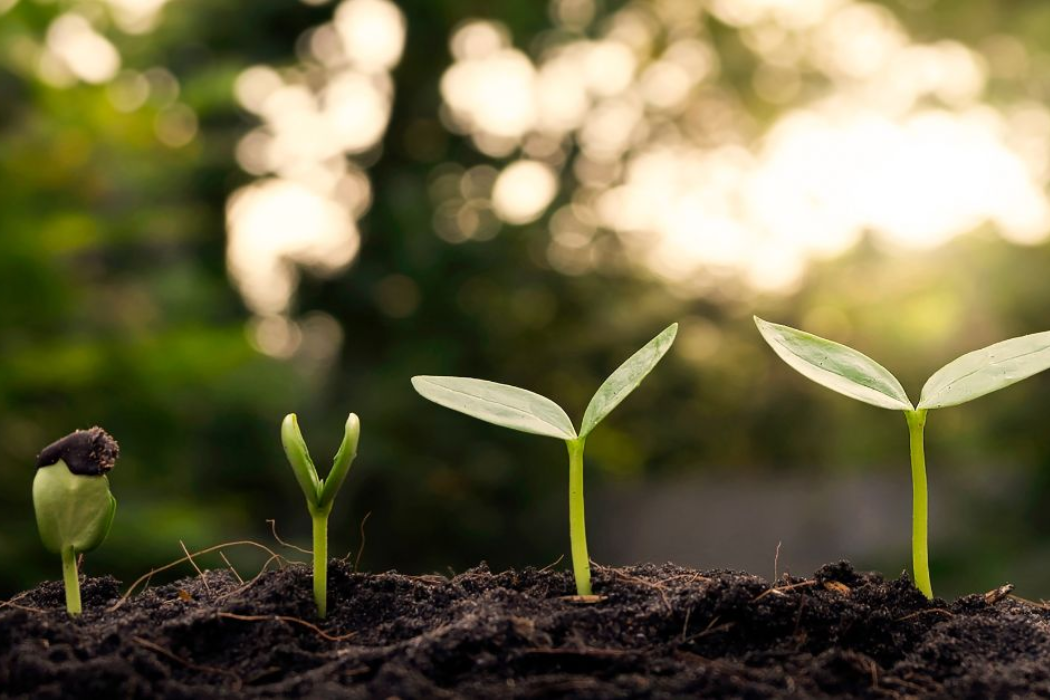
Central to the success of the certification process, which is designed to engage scientists and lab professionals, is the Lab Lead—a key champion who takes on the responsibility of guiding their lab through the certification process.
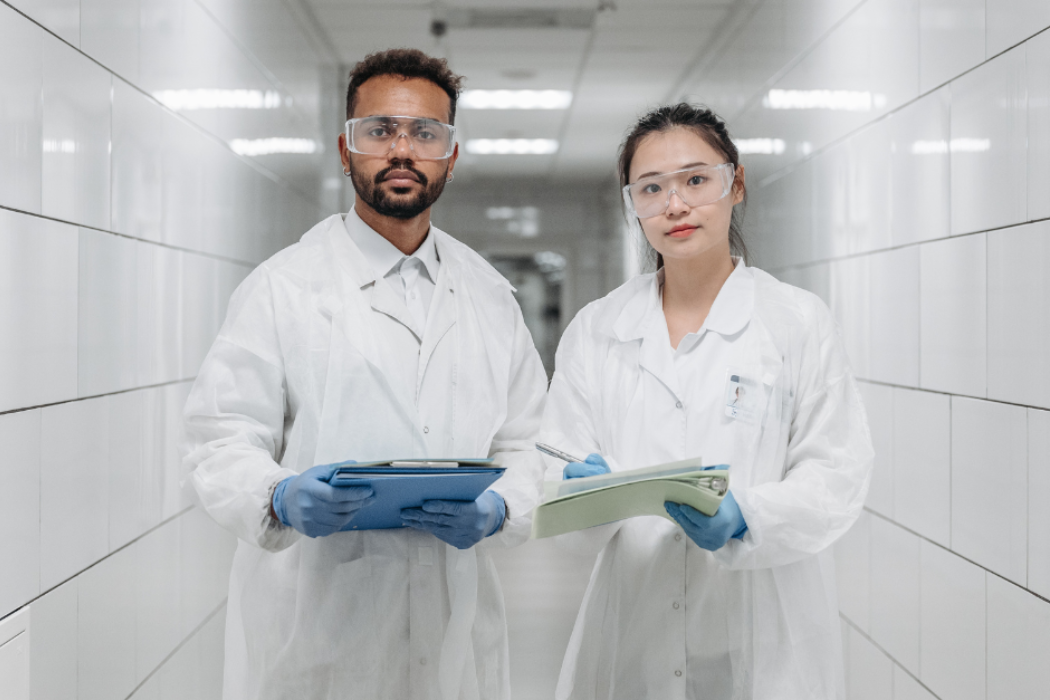
We are proud to announce that our commercial subsidiary, Impact Laboratories, third-party verifier of My Green Lab Certification, has secured $4.95 million in Series A funding, exceeding its target.
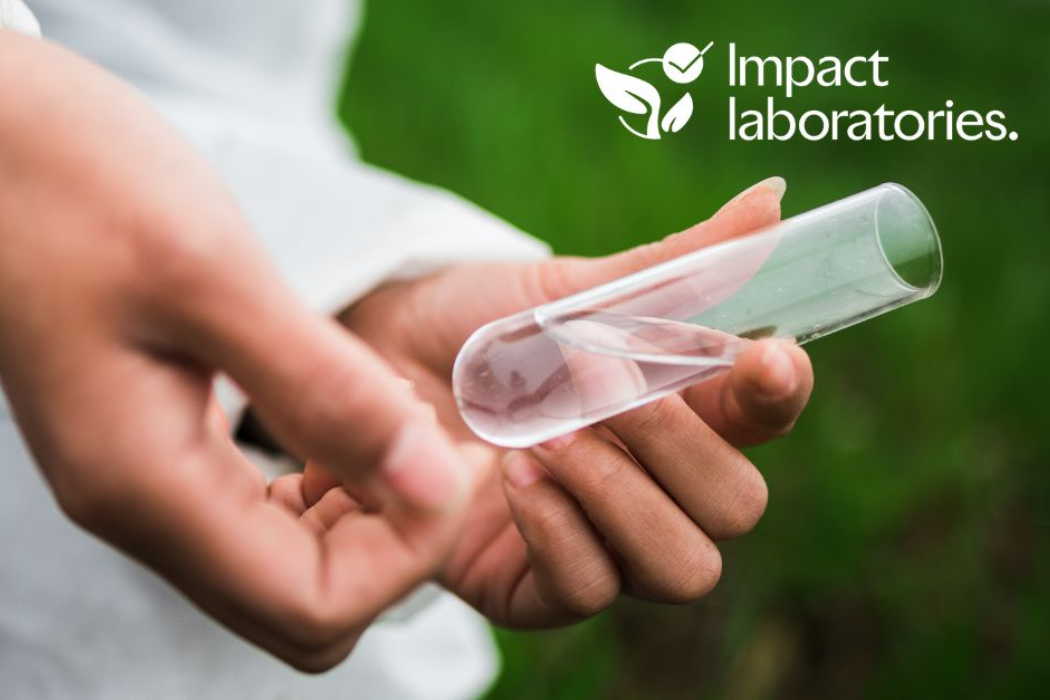
My Green Lab is thrilled to announce the launch of My Green Lab Certification 2.0, the next generation of the world’s most trusted green lab certification!
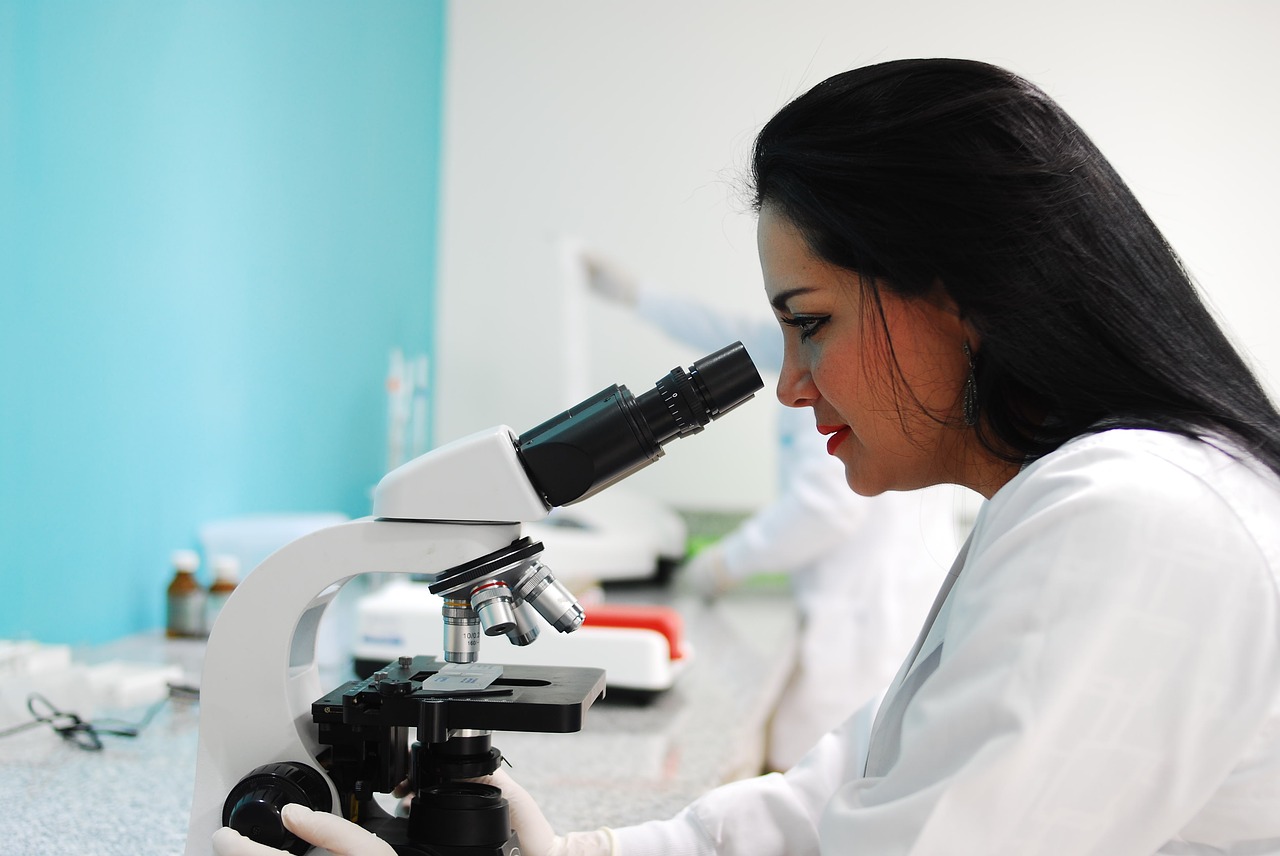
In 2024, My Green Lab and the global green lab community achieved extraordinary milestones, further embedding sustainability into the fabric of scientific research.
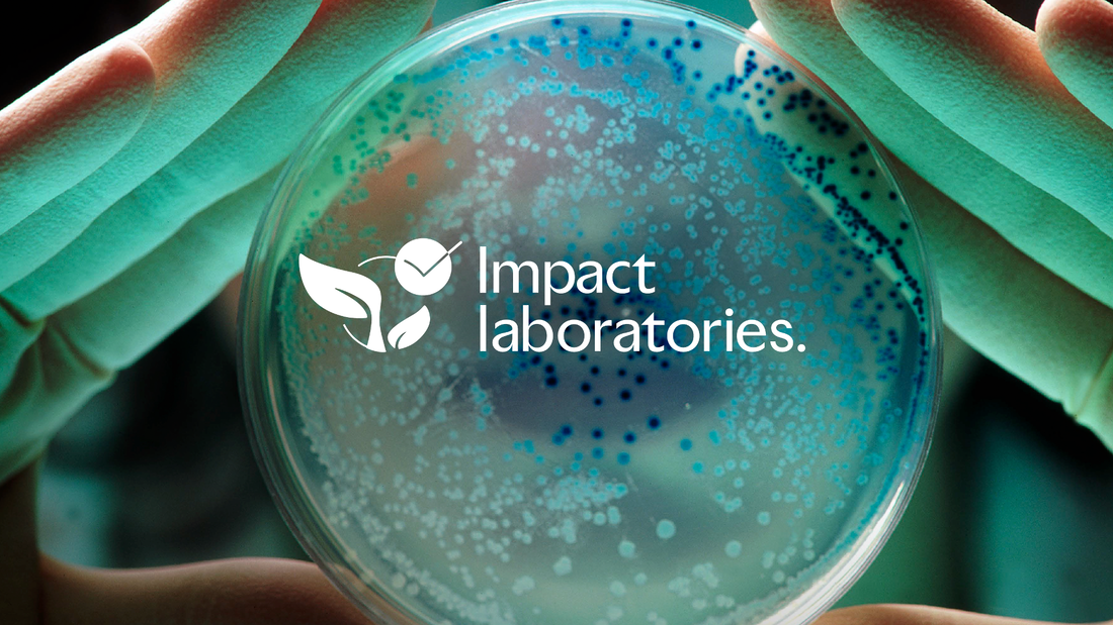
KNAUER's commitment to sustainability has earned it HPLC systems the lowest Environmental Impact Factor (EIF) score in the My Green Lab® ACT® Ecolabel database (as of January 2025).
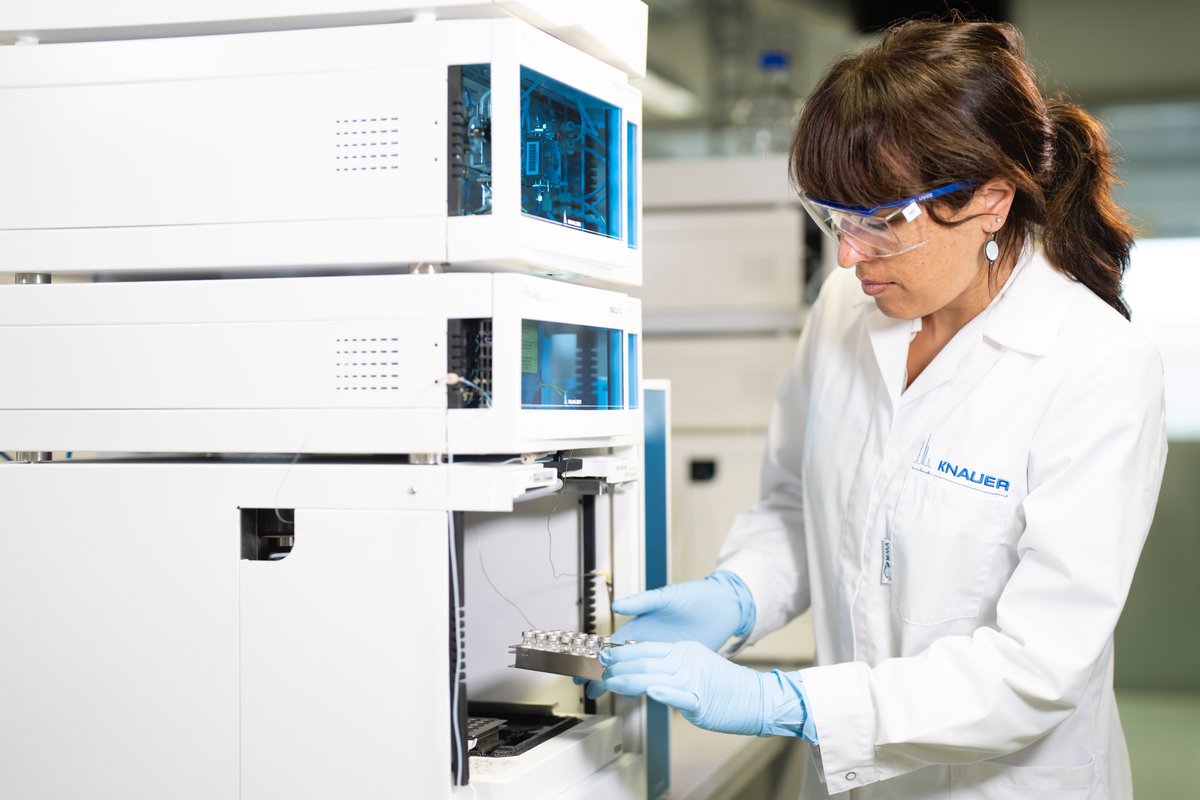
As Ryan embarks on his next chapter as Regional Business Manager for the Spokane Region at Avista Corporation, we take this opportunity to reflect on his journey, achievements, and vision.
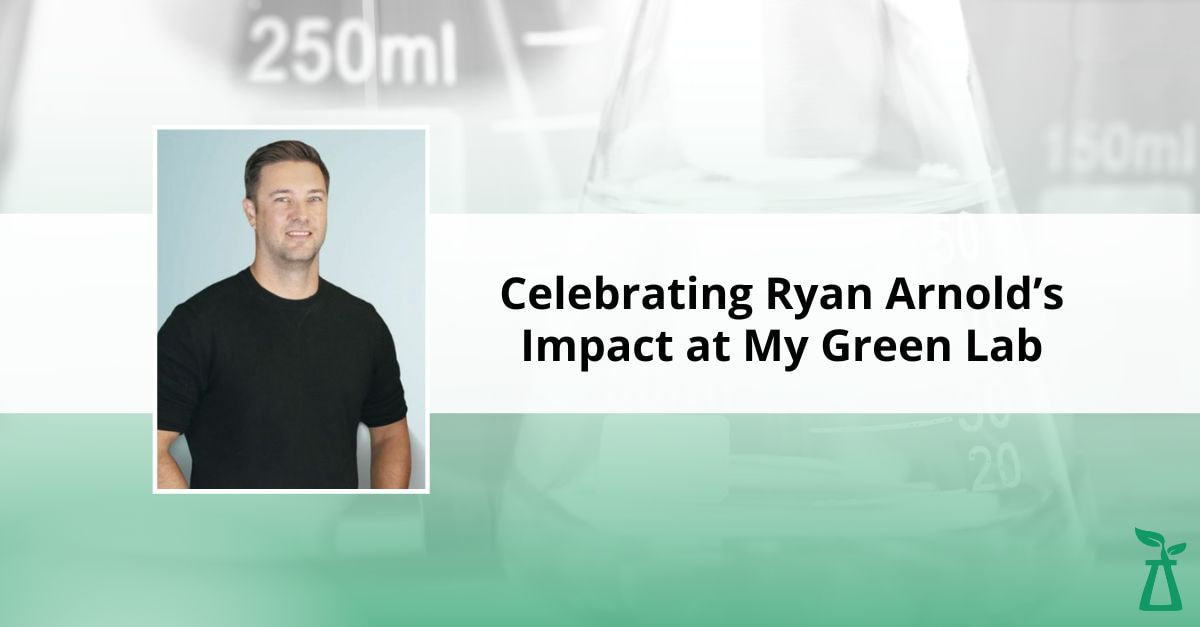